Category
- Products
-
- Contact us
Home » Soft Starters Knowledge » Benefits of soft starters
Benefits of soft starters
Soft starters are solid-state devices that protect AC electric motors from damage caused by sudden influxes of power by limiting the large initial inrush of current associated with motor start-up. They provide a gentle ramp-up to full speed and are used only at start-up (and stop if equipped). Ramping up the initial voltage to the motor produces this gradual start. Soft starters are also known as reduced voltage soft starters (RVSSs).
Applications
Soft starters are used in applications where:
Speed and torque control are required only during startup (and stop if equipped with soft stop).
Reduction of large start-up inrush currents associated with large motors is required.
The mechanical system requires a gentle start to relieve torque spikes and tension associated with normal startup (e.g. conveyors, belt-driven systems and gears).
Pumps are used to eliminate pressure surges caused in piping systems when fluid changes direction rapidly.
Electrical soft starters reduce voltage or current input temporarily by reducing torque. Some soft starters may use solidstate devices to help control the flow of the current. They can control one to three phases, with 3-phase control usually producing better results (see Fig.)
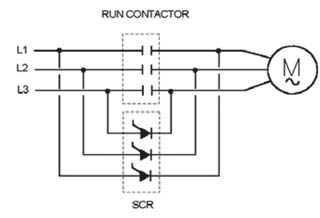
Most soft starters use a series of thyristors or silicon controlled rectifiers (SCRs) to reduce the voltage. In the normal off state, the SCRs restrict current but in the normal on state, they allow current. The SCRs are engaged during ramp-up and bypass contactors are pulled in after maximum speed is achieved. This helps to reduce motor heating.
Benefits of soft starters
Soft starters are often the more economical choice for applications which require speed and torque control only during motor start-up. They are often the ideal solution for applications where space is a concern as they usually take up less space than variable frequency drives.
Applications
Soft starters are used in applications where:
Speed and torque control are required only during startup (and stop if equipped with soft stop).
Reduction of large start-up inrush currents associated with large motors is required.
The mechanical system requires a gentle start to relieve torque spikes and tension associated with normal startup (e.g. conveyors, belt-driven systems and gears).
Pumps are used to eliminate pressure surges caused in piping systems when fluid changes direction rapidly.
How does a soft starter work?
Electrical soft starters reduce voltage or current input temporarily by reducing torque. Some soft starters may use solidstate devices to help control the flow of the current. They can control one to three phases, with 3-phase control usually producing better results (see Fig.)
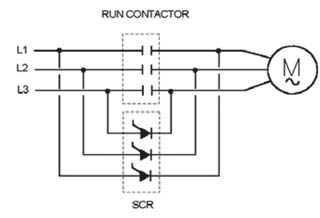
Most soft starters use a series of thyristors or silicon controlled rectifiers (SCRs) to reduce the voltage. In the normal off state, the SCRs restrict current but in the normal on state, they allow current. The SCRs are engaged during ramp-up and bypass contactors are pulled in after maximum speed is achieved. This helps to reduce motor heating.
Benefits of soft starters
Soft starters are often the more economical choice for applications which require speed and torque control only during motor start-up. They are often the ideal solution for applications where space is a concern as they usually take up less space than variable frequency drives.
Post a Comment:
You may also like: